The Role of Welding Examination in Stopping Failures and Enhancing the Longevity of Welded Structures and Components
Welding evaluation is a crucial element in the lifecycle of bonded frameworks, working as a positive step against potential failures that can jeopardize security and functionality. By systematically identifying issues such as porosity or insufficient combination, inspectors can considerably enhance the durability of important parts. The application of varied assessment methods not only guarantees compliance with industry standards however likewise cultivates a robust society of quality guarantee. However, the ramifications of overlooking this essential practice can be extensive, questioning concerning the true influence on architectural stability and long-term efficiency. What are the best techniques that can additionally raise inspection performance?
Relevance of Welding Assessment
Welding inspection functions as a vital safeguard in the stability of welded structures, ensuring that they satisfy stringent security and high quality requirements. The relevance of this process can not be overemphasized, as it plays an essential duty in recognizing prospective issues prior to they rise into tragic failures. By carefully examining welds, examiners can verify adherence to create specifications and regulatory requirements, thereby reducing risks related to structural concession.

Additionally, efficient welding evaluation improves the longevity of parts, as it enables the early discovery of problems that might cause deterioration with time. This aggressive strategy not only extends the service life of welded structures yet also advertises dependability and operational performance. In industries such as building and construction, aerospace, and auto, where safety and security is extremely important, the evaluation process is vital.
Additionally, welding inspection cultivates a society of quality control within companies, encouraging adherence to ideal methods and continuous renovation. By purchasing comprehensive examination procedures, companies can boost their track records and maintain consumer count on. Ultimately, the relevance of welding assessment hinges on its ability to maintain safety, high quality, and longevity in bonded frameworks, making it an essential part of engineering honesty.
Common Welding Flaws
Several usual welding problems can endanger the integrity of bonded structures, bring about prospective failings if not addressed. Amongst these issues, porosity is among one of the most prevalent, identified by the presence of little gas pockets entraped within the weld metal. This can dramatically compromise the joint, causing lowered structural honesty.
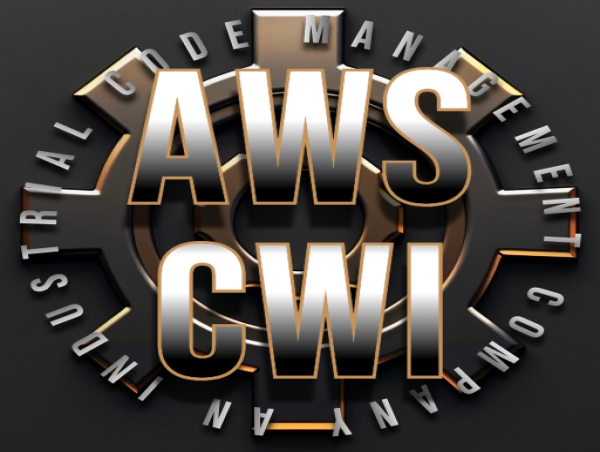
One more issue is insufficient combination, which happens when the weld steel falls short to sufficiently fuse with the base product or previous weld layers. This absence of bonding can produce weak factors that might stop working under stress and anxiety. Absence of penetration refers to inadequate depth of weld metal, preventing the joint from achieving its intended strength.
Cracks can also establish throughout the welding process, typically because of fast cooling or unsuitable welding parameters. These cracks may propagate under lots, bring about catastrophic failings. Additionally, excessive spatter can hinder the weld's top quality by presenting contaminants.
Inspection Techniques and Techniques
Reliable assessment methods and techniques are vital for making sure the stability and durability of welded structures. A comprehensive inspection program employs a range of non-destructive screening (NDT) techniques to discover prospective next page problems without jeopardizing the bonded elements. Among the most commonly made use of methods are visual inspection, ultrasonic screening, radiographic screening, magnetic bit testing, and dye penetrant screening.
Aesthetic evaluation works as the very first line of defense, enabling inspectors to recognize surface defects such as splits, imbalances, or incomplete blend. Ultrasonic screening utilizes high-frequency acoustic waves to find internal problems, providing thorough details regarding the product's integrity. Radiographic screening uses X-rays or gamma rays to envision the interior framework of welds, making it possible for the recognition of gaps and incorporations.
Magnetic bit testing works for detecting surface and near-surface stoppages in ferromagnetic materials, while dye penetrant screening highlights surface-breaking issues using colored dyes. Each method has its special benefits and constraints, requiring a critical mix to achieve comprehensive assessment insurance coverage. Applying these techniques systematically guarantees that any type of prospective issues are recognized early, cultivating the integrity and resilience of welded structures.
Influence On Structural Integrity
The honesty of a framework is significantly affected by the top quality of its bonded joints, as they offer as crucial points of stamina and stability. Badly performed welds can lead to stress focus, exhaustion failings, and eventually, devastating structural collapse. The dependence on welding as a key ways of joining materials demands strenuous examination procedures to guarantee that welds meet well-known criteria and specs.
Shortages in weld quality, such as insufficient blend, fractures, or porosity, can compromise the mechanical buildings of the joint, view publisher site affecting load-bearing capability and total performance. When these problems go undiscovered, they can propagate under operational stress and anxieties, causing a decline in structural integrity gradually. Regular and thorough examinations are crucial in identifying these weak points prior to they intensify right into considerable failures.
Additionally, the impact of environmental aspects, such as rust, can be worsened by insufficient welding practices. Thus, ensuring high-grade welding through cautious inspection not just advertises immediate structural reliability however additionally extends the life span of parts. Welding Inspection Milwaukee. Ultimately, the investment in appropriate welding inspection is a necessary strategy for securing versus structural failures, consequently boosting the longevity and safety of welded frameworks
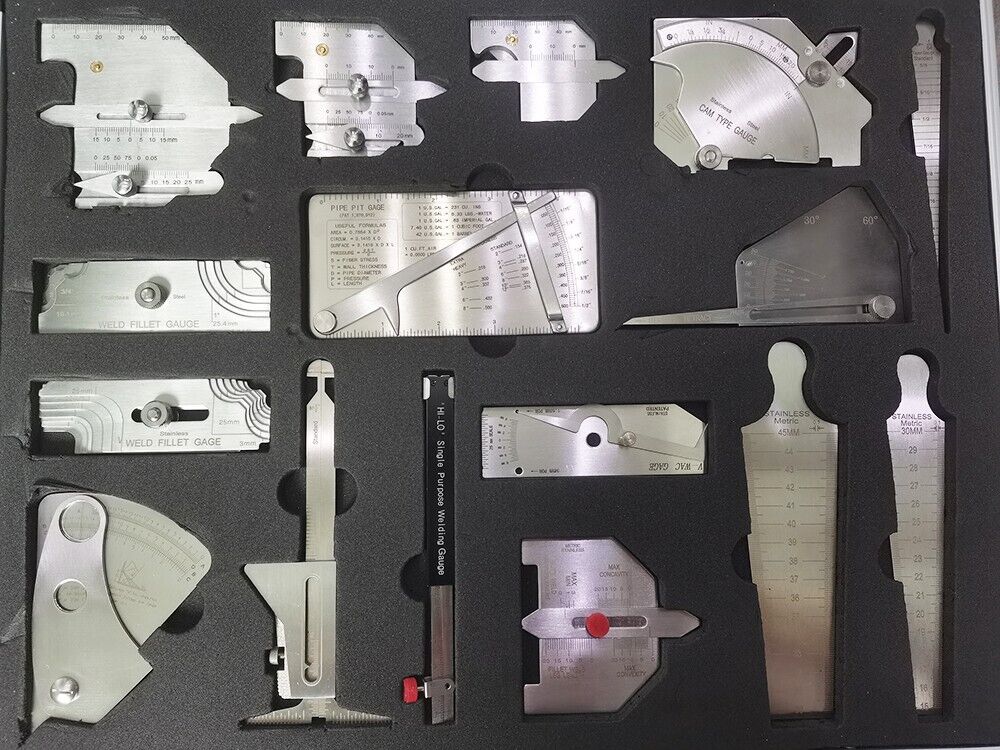
Ideal Practices for Effective Examination
Implementing systematic inspection methods is essential for ensuring the integrity of welded joints. Effective inspection starts with the growth of thorough lists customized to the details welding procedures and products included. These checklists should encompass aesthetic inspections, non-destructive screening (NDT) approaches, and documents testimonial to make sure that all elements of the welding process are inspected.
Training and certification of inspection personnel are essential parts of an effective evaluation program. Inspectors must be fluent in different NDT methods, including ultrasonic, radiographic, and magnetic fragment testing, to accurately recognize flaws such as fractures, porosity, and incomplete combination.
Prompt examinations ought to be scheduled at numerous stages of the welding process-- pre-weld, throughout welding, and post-weld-- to catch any possible problems early. Additionally, keeping comprehensive documents of assessments promotes accountability and facilitates future examinations.
Conclusion
Welding inspection is crucial for determining defects and making sure the stability of bonded frameworks. By employing numerous evaluation strategies, potential problems can be found early, thus protecting against catastrophic failures and improving the long life of components. The execution of ideal practices in assessment fosters a culture of quality control, guaranteeing conformity with layout specs and governing standards. Ultimately, efficient welding examination not only safeguards structural stability but additionally adds considerably to the general dependability and resilience of welded joints.
Welding evaluation is a crucial part in the lifecycle of bonded structures, serving as a proactive action versus prospective failures that can compromise safety and security and capability.Welding assessment serves as a crucial secure in the stability of welded structures, making certain that they satisfy strict safety and top quality criteria. Welding Inspection Milwaukee. Inevitably, the relevance of welding assessment lies in its capacity to maintain safety, top quality, and durability in welded structures, making it a fundamental part of engineering honesty
Eventually, the investment in proper welding examination is a necessary technique for protecting against architectural failures, therefore improving the durability and safety of bonded frameworks.
Welding assessment is vital visit this page for identifying flaws and guaranteeing the honesty of welded frameworks. Welding Inspection Milwaukee.